Essential Pipeline Welding Inspection Tips for Quality Control
How can one ensure the quality of these welds that attach the pipeline areas? By comprehending the essential pipe welding evaluation tips, experts can avert possible hazards, lower expensive repairs, and maintain the reliability of these essential facilities.
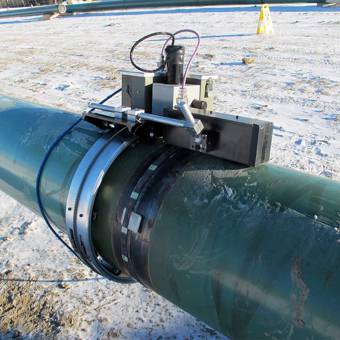
Significance of Welding Inspection
Welding examination plays an important function in ensuring the architectural integrity and safety and security of pipeline systems. By diligently analyzing welds, inspectors can determine any type of issues or flaws that could endanger the stability of the pipeline. These inspections are crucial for protecting against leakages, ruptures, and other possibly catastrophic failings that can lead to ecological damage, monetary losses, and also loss of life.
The value of welding inspection can not be overstated, as the top quality of welds directly affects the total performance and durability of the pipe. Through non-destructive screening methods such as aesthetic examination, ultrasonic testing, radiography, and magnetic bit testing, inspectors can identify defects that may not be noticeable to the naked eye. By determining and resolving these issues beforehand, welding inspection assists to make sure that pipes meet market requirements and governing requirements.
Eventually, welding assessment is a crucial element of quality control in pipe building, maintenance, and repair (Pipeline Welding Inspection). By maintaining extensive examination standards, industry experts can alleviate dangers and support the security and reliability of pipe systems
Typical Welding Defects
Among the difficulties faced in pipe welding, usual problems can dramatically impact the structural honesty and efficiency of the welded joints. Fractures in the weld can circulate over time, compromising the architectural integrity of the pipeline. Spotting and attending to these usual defects with detailed evaluation and top quality control procedures are essential for guaranteeing the dependability and safety and security of pipe welds.
Inspection Methods for Pipelines
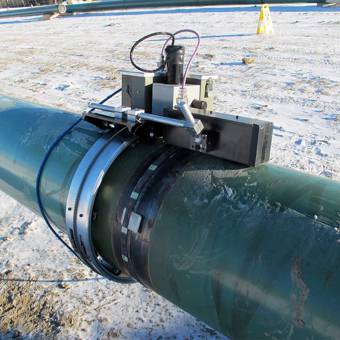
Non-destructive screening (NDT) techniques such as radiographic testing, ultrasonic screening, magnetic particle screening, and liquid penetrant screening are typically made use of in pipeline welding inspection. Visual evaluation is also vital in pipeline welding to recognize any kind of noticeable problems or gaps. Additionally, computerized inspection techniques using innovative modern technologies like robotics and drones are progressively being used to enhance the effectiveness and accuracy of pipeline examinations.
Making Certain Quality Control Requirements
To maintain rigorous top quality assurance requirements in pipeline building, careful adherence to developed sector methods and standards is important. Quality assurance in welding procedures calls for a thorough approach encompassing various stages of pipeline construction. Executing a robust quality monitoring system that consists of normal audits and evaluations can additionally improve the general high quality assurance standards in pipeline welding.
Avoiding Costly Repairs
Given the crucial importance of maintaining rigorous top quality guarantee requirements in pipeline building and construction, an aggressive Continue technique to avoid costly repairs is essential. By applying detailed assessment protocols throughout the welding process, possible problems can be identified and fixed beforehand, ultimately conserving both time and money. One essential facet of avoiding expensive repair work is making sure that welders are appropriately trained and licensed, as this considerably minimizes the chance of faulty welds that may bring about future failings. Additionally, utilizing sophisticated evaluation techniques such as non-destructive screening can help identify any type of defects or variances in the welds before they rise into significant issues. Normal maintenance checks and surveillance of environmental variables that could influence the integrity of the pipe are additionally vital in avoiding pricey repair work. By spending in preventative steps and focusing on quality assurance at every phase of the pipe welding process, firms can minimize the threat of expensive repair services and ensure the long-lasting integrity of their infrastructure.
Verdict
In final thought, adherence to proper welding assessment techniques is important for making certain the top quality and integrity of pipelines. By recognizing typical welding issues and executing extensive evaluation procedures, costly Learn More Here repair work can be prevented, and quality control criteria can be met - Pipeline Welding Inspection. It is essential for pipeline welders to prioritize inspection treatments to preserve the safety and integrity of the facilities they are servicing
The relevance of welding assessment can not be overstated, as the top quality of welds directly impacts the total performance and long life of the pipeline. Non-destructive screening (NDT) methods such as radiographic screening, ultrasonic testing, magnetic fragment testing, and fluid penetrant testing are commonly used in pipeline welding assessment. Visual assessment is also crucial in pipeline welding to recognize any noticeable defects or discontinuities. Furthermore, computerized evaluation strategies utilizing innovative technologies like drones and robotics are increasingly being utilized to boost the efficiency and accuracy Pipeline Welding Inspection of pipe evaluations.In final thought, adherence to correct welding evaluation strategies is essential for making sure the top quality and integrity of pipelines.